This blog is part of InfoDesk’s latest series which explores the state of the life science supply chain in light of COVID-19. You can read our other blogs here or download the latest InfoGraphic here.
As the life sciences industry is at the forefront of the battle against COVID-19, a strong and efficient manufacturing process is needed. Recent news has reported a flurry of headlines that have noted various shortages and disruption of manufactured drugs, devices and personal protective equipment. Currently, various industry stakeholders and thought leaders are suggesting mitigating strategies to enact in order to stem any interruption of the critical life sciences supplies needed by the world.
In a survey of pharmaceutical professionals conducted by Lachman Consultants, it found that over 45% of responses indicated a “very concerned” status regarding the integrity of their company’s supply chain. Only about 11% were not concerned at all regarding supply chain disruptions. The issue of supply chain integrity has been such a concern that the FDA published a guidance document on how to report shortages during the COVID-19 emergency. Likewise, the European Medicines Agency set up a single point-of-communication to report any pharmaceutical shortages (or even suspected shortages).
In fact, the CEO of Regeneron Pharmaceuticals, Len Schleifer, said in a recent interview on CNN that the U.S. manufacturing capacity to fulfill orders for COVID-19 therapies and vaccines is “limited.” He further explained that although various companies are scaling up production in their facilities, this effort may still not be enough to meet the high demand.
Examples of Supply Disruption
Assorted life sciences companies have experienced manufacturing supply chain challenges and concerns within recent months due to the COVID-19 pandemic. Many companies that had factories in China closed them during the outbreak, causing a ripple of manufacturing disruptions. Examples of life science companies reporting such disruptions include Lonza reporting about a few raw bulk supplies being delayed and West Pharmaceutical Services indicating that they had especially noticed delays in air and sea supply shipments. Constellation Pharmaceuticals also noted some supply chain disruptions but stated they did not impact company timelines.
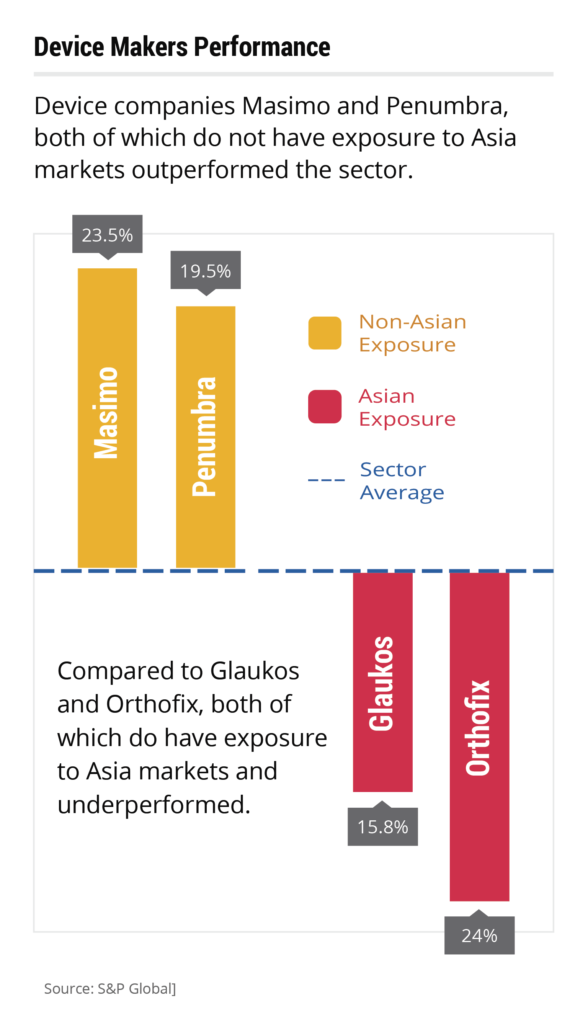
Various reports have shown that pharmaceutical and medical device companies that have minimal exposure to Asian supply chain channels have outperformed firms that had exposure to that region. S&P Global finds that medical device manufacturers Masimo and Penumbra, which did not have Asian exposure, outperformed the sector by 23.5% and 19.8%, respectively. Two device manufacturers that did have exposure to Asia, Glaukos and Orthofix, experienced underperformance in the sector, by 24.6% and 15.8%, respectively. Supply Chain Dive agrees that long-distance supply chains may be one of the causes of problems among pharmaceutical companies and medical device makers that experienced supply shortages. Michael J. Alkire, president of group purchasing organization Premier, goes on to suggest in the article that this exposure can be mitigated by increasing the amount of US and near-shore manufacturing, reducing the length of these supply chains.
Even some manufacturing facilities that have reopened aren’t necessarily operating at a 100% capacity. Within China, GlobalData reported that although many factories have gone back to full capacity, others still only operate at 50% to 80% capacity. Reduced manpower, resulting from travel and other challenges, is a contributing factor for this.
Companies Responses to Manufacturing Supply Chain Challenges
Life sciences companies have been responding, using an array of strategies, to manage the challenges being experienced in the worldwide supply chain due to the pandemic. Accord Healthcare worked with the UK government in order to obtain the rights to build expanded manufacturing capacity to deliver medicines at the accelerated pace needed. A press release from the firm stated:
“In response to growing UK and global demand for vital COVID-19 drugs, including ICU medicines like cisatracurium, midazolam and paracetamol, we are working closely with regulatory agencies to accelerate approval for a large new manufacturing facility that can further increase output of these medicines.”
Some companies are partnering with other firms for expanded manufacturing capacity. Gilead stated that they are building a “geographically diverse consortium” of pharmaceutical/chemical facility collaborators in order to ensure proper supplies of remdesivir (for COVID-19 therapy). Another company using this strategy is Co-Diagnostics, which makes an FDA approved COVID-19 test. They partnered with Promega in order to increase their manufactured volume of tests to bring to the market.
Many pharmaceutical manufacturers have proactively sent “status” press releases and enacted policies to deal with any potential supply chain disruption. Sanofi indicated that they were closely collaborating with suppliers and enacting continuity strategies to ensure a solid supply chain. Eli Lilly also published a press release stating that they experienced no drug shortages but indicated that they had enacted new precautions in some of their facilities.
Experts Offer Insights on Mitigation Strategies
Industry experts have provided guidance on ways that life sciences companies can manage supply chain challenges. A recent International Society for Pharmaceutical Engineering (ISPE) webinar on supply chain management for the pharmaceutical industry provided numerous insights into how companies can ensure overall supply chain flow. Overarching themes of the advice include enacting continuous communication and collaboration with employees as well as supply vendors and government officials. By implementing active and efficient ways to work with all stakeholders involved in the supply flow, life sciences companies can help to maintain continuous supply.
Analysts have also provided guidance regarding ensuring proper supplies for clinical trials. This issue is particularly concerning since so many new COVID-19 clinical trials are being initiated and need an uninterrupted supply of drugs. GlobalData, which keeps watch of clinical trial interruptions, cited that 432 clinical trials had been suspended or disrupted due to COVID-19 just within a 4-day analysis of news and status checks. They stated, “Country-wide lockdowns as a countermeasure against COVID-19 have severely affected the clinical development of new agents…” Although issues like patient enrollment and staff safety are also of concern during clinical trials, adequate manufacturing and delivery of therapies to the trial sites is an important concern. Parexel also addressed the topic of maintaining adequate drug supplies to clinical trials, suggesting that interactive response technology (IRT) can have an important role in securing medications within these studies.
Baker Tilly, which offers a report with a particular focus on maintaining clinical trial supply chain efficiency in the wake of COVID-19, suggests the following steps to mitigate the problem of supply disruption:
- Expand the numbers of locations of manufacturing sites
- Initiate efforts to stockpile needed resources
- Create requirements for device makers to publicly report shortages
They go on to suggest that the life sciences industry may be the model that other industries follow if drug and device companies succeed in their efforts to overcome supply chain difficulties. Their report states:
“Life Sciences will be the global steward leading the world economy through this crisis…”
Conclusion
Overall, it appears that constant fact-finding surveillance of the supply chain is the key to making the decisions needed to address supply problems. An article from MedCity News actually states that life sciences companies should “prepare for increased disruption” and that access to quality information is the most important process to implement. The guidance from this publication suggests that the vast visibility of a company’s supply chain is critically important to manage any interruptions. The right visibility tools can help companies to communicate and collaborate with suppliers and transportation service providers in a timely manner in order to improve, and potentially fix, any supply disruptions.
Working in concert with internal stakeholders, external suppliers and regulatory bodies, life sciences companies are bolstering their efforts to avoid supply chain disruptions. Never-ending agility may be the pathway to success in this environment of uncertainty, with the accompanying roles of accurate information and good communication being undeniably connected, both in terms of navigating manufacturing disruptions, specifically, as well as the larger challenge of stabilizing the entire supply chain, worldwide.
COMMENTS